|
|
|
 |
|
|
|
|
|
|
|
|
|
|
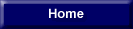 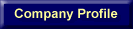 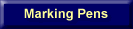 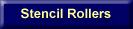 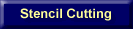 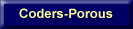 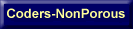 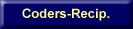 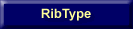 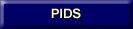 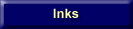 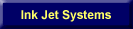 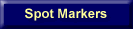 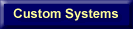 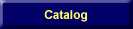 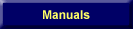 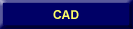 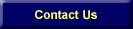 |
|
 |
|
|
|
|
|
|
|
|
Universal
offers custom designed marking systems to fill specific application requirements.
This service can involve simple modifications to standard products or completely
custom designed automated marking and control systems. The items listed below
are a few of our previous custom design projects and are intended to give our
customers a feel for the scope of our capabilities. If you are searching for
a solution for a specific application problem, please contact our Engineering
Department for assistance. |
|
|
|
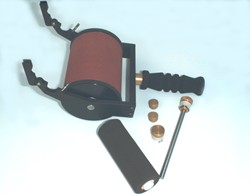 |
|
|
|
|
Large
Hand Held Roll Coder This unit was custom designed to satisfy
a customer's requirement for a hand held roll coder with a 5.5" print
width and a 15" circumference print drum. Since the application required
the use of a non-porous Mil Spec stencil ink, a quick change, eccentric
adjustable ink roll mount was used to facilitate removal and storage of
the rolls in a sealed container after use. |
|
|
|
|
|
|
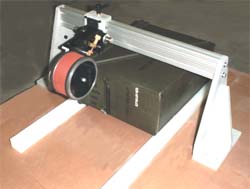 |
|
|
|
|
Custom
Coder Mounting Assemblies Commonly used to gang mount Non-Porous
Coders in web printing applications, these mounting assemblies include an extruded
aluminum bridge to span the conveyor or web line. Individual saddle mounts for
the coders with a ratchet handle lock enable quick lateral positioning of the
coders. This particular system was used with a single coder to apply content
information on an ammunition container. |
|
|
|
|
|
|
|
|
|
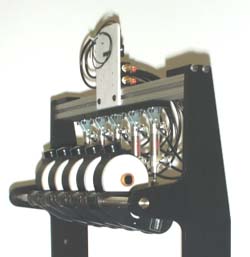 |
|
|
Web
Printing With Gang Mounted Non-Porous Coders This system was designed
to apply dense black stripe marks for optical sensing on a paper web. Five customized
Non-Porous Mini-Coders were mounted on a common shaft and pneumatically raised
and lowered to apply the marks at the required locations on the web. A PLC based
control with an encoder input tracked the web travel and engaged the coders
at the programmed intervals. The system included a hand held programming unit
to enable the operators to change the program parameters in the field. |
|
|
|
|
|
|
|
|
|
|
|
|
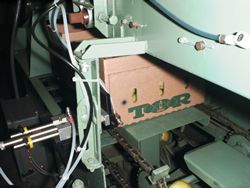 |
|
|
Carton
Identification System Using Color Coded Spot Marks An agriculture
industry application required unique carton coding to identify cartons packaged
on specific filler machines for downstream sorting. A USMR-20AF Micro-Spray
Marker mounted on a pneumatic slide was used to apply 1/2" diameter spot
marks on the front side of the cartons during the filling operation. A PLC based
marking system controller was interfaced with the filler control to trigger
the system operation. When an initiate signal was received from the filler control,
the slide extended, the mark applied, and the slide retracted before the carton
left the filler. |
|
|
|
|
|
|
|
|
|
|
|
|
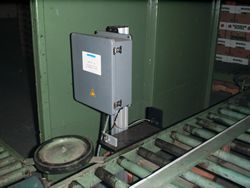 |
|
Color
Detection Scanning System Cartons moving at 270 fpm are scanned with
Universal's Color Detection System which looks for the 1/2" diameter colored
spot marks on the cartons which were applied by the marking system shown above.
Cartons with the target marks are kicked off the main conveyor onto the appropriate
palletizing conveyor. For highest reliability, fiber optic sensors look for
the code marks only in a discreet location on the cartons, ignoring even identical
colors in other areas of the carton. A PLC based controller with a hand held
programming unit enables operators to adjust for line speed changes and kicker
timing functions. |
|
|
|
|
|
|
|
|
|
|
|
|
|
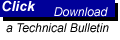 |
|
|
|
|
|
|
|
|
|
|
|
|
|
|
|
|
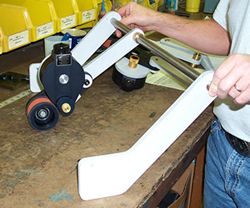 |
|
Extension
Arm Mounts Typically used for printing directly on master rolls of
plastic film, metals etc. The selected coder is modified by removing the standard
mounting bracket, column and spring tension assemblies. A custom extension arm
is attached to the coder baseplate to extend the reach and travel of the coder.
Custom mounting brackets are designed to provide easy installation on the parent
equipment. As the web material is pulled from the roll, the extension arm, which
pivots on a stainless steel shaft, allows the coder to ride on the surface of
the master roll and print on the web material as it is being unwound. The coder
remains in contact with the surface of the master roll, following the diminishing
diameter of the roll down to the core. |
|
|
|
|
|
|
|
|
|
|
|
|
|
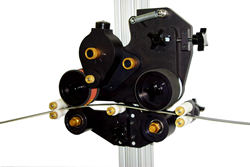 |
|
Custom
Narrow Web Coding System This system was designed to print codes
on continuous web materials that are too narrow to engage the friction drive
bearers on our standard Non-Porous Coders. A floor mounted stand includes a
height adjustable idler roll assembly which guides the web through the coder.
A friction driven offset roll mounted upstream of the print drum keeps the print
drum rotating at the same surface foot velocity as the web. Printing die contact
pressure is fully adjustable on the fly for optimal print quality. Interchangeable
print drums and offset drive rolls provide both 12" or 15" circumferences
and a 1" maximum print width. |
|
|
|
|
|
|
|
|
|
|
|
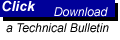 |
|
|
|
|
|
|
|
|
|
|
|
|
|
|
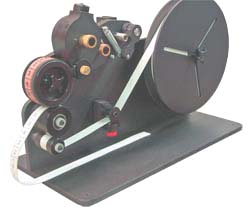 |
|
Custom
Nylon Web Printing System This system was designed for a sail manufacturer
to print assembly registration marks and numbers on a nylon web material at
specific intervals. A custom print drum was produced to provide the exact repeat
interval required. A full roll of web material would be loaded on the reel and
varying lengths would be pulled off as needed for the assemblies. |
|
|
|
|
|
|
|
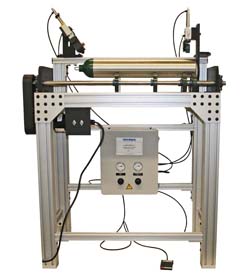 |
|
Custom
Cylinder Printing System This system was designed to apply a solid
black stripe around the spherical end of a compressed gas cylinder. The cylinders
are loaded onto a set of cradle rolls which rotate at approximately 30 RPM.
A foot pedal switch is pressed which activates the 5 - 6 second marking cycle.
This PLC controlled system accommodates cylinders of various diameters and
lengths.
Similar systems have been
built with Non-Porous Roll Coders to apply text around the circumference of
missile bodies and other ordnance items. |
|
|
|
|
|
|
|
|
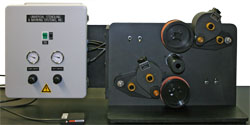 |
|
 |
|
Custom
Two Color Ordnance Printer This system was designed to print both
a brown stripe and black text on an ordnance cannister. The empty cannister
tube is loaded on a rotating mandrel and both printers engage the part simultaneously
when a foot pedal switch is pressed. This system provides a 3 second, two color,
cycle time. |
|
|
|
|
|
|
|
|
|
|
|
Custom
Pneumatically Controlled Non-Porous Mini-Coder This system was designed
to operate in conjunction with an optical inspection system for a continuous
web application. When a defect area of the web is indentified, a 24 VDC signal
is sent to the printer which would then lower into contact with the web and
print DEFECT AREA repeatedly until the electrical signal was turned off. This
system can also be used to print a continuous stripe on a web to indicate end
of roll or provide similar functions. Multiple units can be mounted on a common
extruded aluminum bridge. |
|
|
|
|
|
|
|
|
|
|
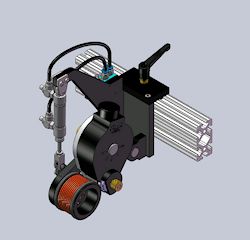 |
|
|
|
|
|
|
|
|
|
|
|
|
|
|
|
|
|
|
|
|
|
|
|
|
|
|
|
|
 |
 |
 |
 |
 |
 |
 |
 |
 |
 |
 |
 |
 |
 |
 |
 |
 |
 |
 |
 |
 |
 |
 |